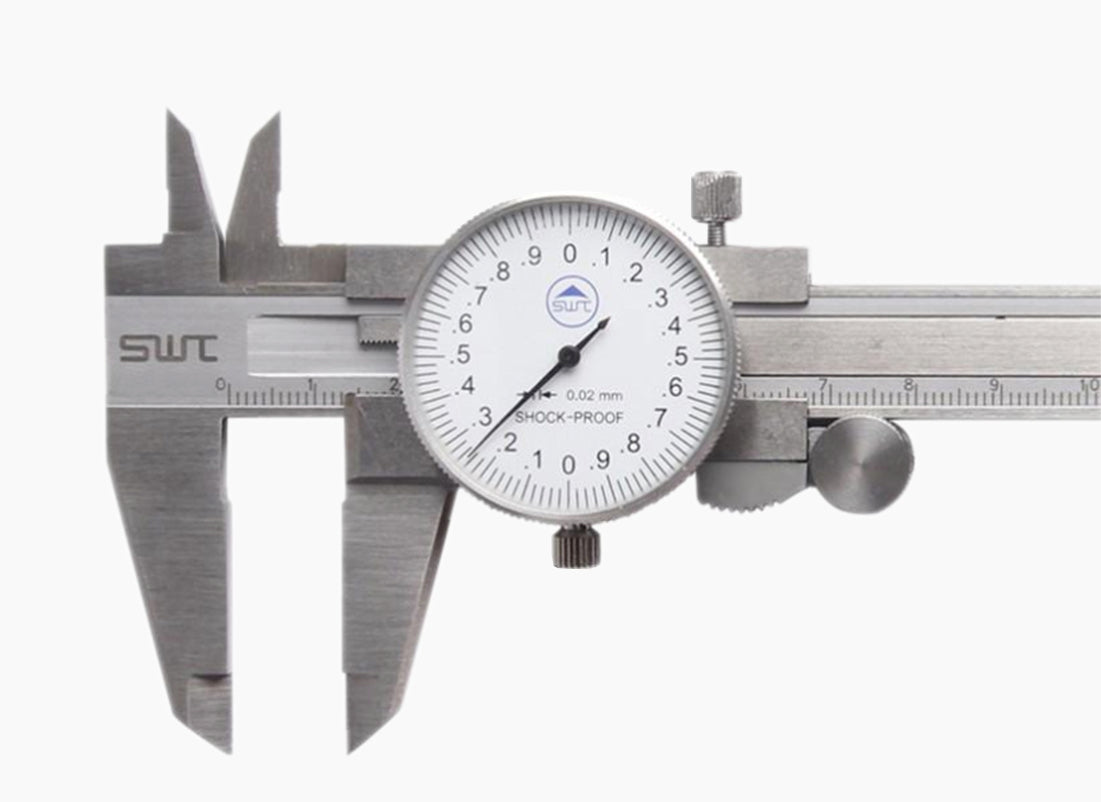
Denali Ski Design
Here at Denali, we have a simple rule when it comes to testing new design concepts and building skis - if it makes sense from an engineering perspective, we’ll try it. Once a concept can pass that test, things get serious.
Design starts with a solid understanding of the hydrodynamics involved, but that is only part of the equation. More broadly, one must understand how we need the ski to perform in order to run more buoys, at shorter lengths and faster speeds. A unique byproduct of our scientific approach to slalom skiing was the development of a much deeper, significantly more evolved understanding of the true dynamics of all parameters at work within the slalom course.
We felt that we couldn’t define the parameters of a ski without a fundamental understanding of skiing itself viewed through the lens of science.
After we know a new design concept is consistent with our theories of skiing, and it also makes solid hydrodynamic sense, we can incorporate the feature into the design. Most manufacturers will make a small change by modifying an existing ski. If, for instance, they feel the ski needs to have a wider tail, the easiest thing to do is to cut the tail of an existing ski in half, widen it, and bond it back together. The test skier(s) then ride the ski to decide if the changes are an improvement or not. The problem with this method is that splitting the tail of a ski changes more than just the width profile, as the carbon laminates are forced into a new wider shape. Longitudinal and torsional flex are impacted dramatically. Rocker can be impacted, as it is difficult to prevent the ski from twisting and deforming. Dampening characteristics and concave depth are also subject to change. So, how are the ski testers to know if the change in width is actually the parameter responsible for the resulting changes in the ski's performance?
At Denali we take a different approach. Eliminating the variables is the only way to truly test a new design concept. Instead of making modifications to an existing ski, we start from scratch. This begins at the computer. We generate a new 3D computer model (CAD), based on the design of the current ski. The proposed design changes are then applied to the design, without disrupting any other variables. Then, we generate the machine tool path to cut a prototype mold on our own custom built 3-axis computer controlled CNC milling machine. From there, we can build a new ski while maintaining the exact desired flex and torsion properties. Only then can we take two nearly identical skis to the lake and scientifically test the new design concept against its baseline counterpart. This design process is something we have perfected. It allows us to go from a completely new computerized design, to a functional prototype ski on the water, in less than 48 hours! This allows us to iterate the design much faster and more precisely than any other company. The ability to build literally anything we can dream up allows us to explore the limits of ski design that no method of hand tuning could ever achieve. Thus, our skis can evolve faster than ever.
So what does that mean for you? It means that you can be confident that the ski you receive has passed many rigorous tests, and is engineered and optimized to help you ski your absolute best. You never have to worry about gimmicks, tricks, hype, or other marketing BS with our skis. If a design feature is on our skis, it’s because it will make you ski better, that’s it. Our goal is to make sure your ski never holds you back, and you can reach your full potential on the water.